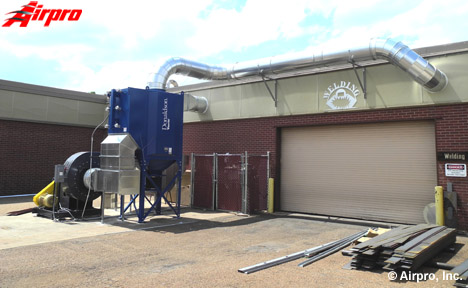
Application: Air Filtration System Upgrade with Auto Dampers
Dust Type: Welding Smoke and Grinding Dust
Location: Colorado
Application: Vocational Tech Center Welding/Metalworking Department required ventilation/air filtration system upgrade in order to meet safe interior operating conditions.
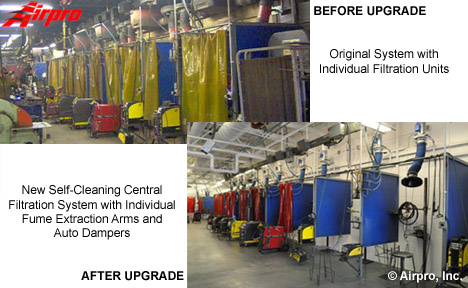
Existing air filtration system consisted of (10) 2 hp, Lincoln Brand Self-Contained Intermittent Duty Air Filtration Units with manual clean cartridge filters and (2) articulated fume exhaust arms per filter unit. The heavy smoke load rapidly filled manual clean filters with particulate which increased filter pressure drop and reduced airflow at individual hoods.
Replacement filters were costly and the replacement task was tedious. Operator breathing zones exposures increased to unsafe levels.
Dust Collection Equipment Solution Selection: (1) Donaldson/Torit Model DFO 3-12 Continuous duty cartridge filter dust collector, (1) AirPro Fan Co Model IEAH 365 Blower, 30 hp, clamping ductwork system, (20) Nederman Telescoping Fume Exhaust Arms with auto dampers and current sensors, Donaldson/Torit Auto-Lok Safety After Filter and VFD electrical control. Cartridge Filters were Donaldson/Torit Ultra-Web Flame-Retardant type.
Airflow/Static Pressure: 8000 cfm @ 16” s.p.
Application Solution:
Due to limited electrical availability, the system was designed to power any 10 booths operating simultaneously. This was accomplished by using Nederman Auto Dampers controlled by current sensors located at each welding machine that open/close auto gates when welding machine current is detected. This plan provided for a 50% smaller filter unit and corresponding h.p. reduction because all positions do not operate simultaneously.
New DFO self-cleaning dust collector clean filters in place while the system operates. This design keeps more constant airflow to hoods, prolongs cartridge filter life thereby reducing filter replacement costs and task frequency. The combination of VFD, auto dampers and current sensors control airflow so all open dampers to fume exhaust arms receive constant airflow. The telescoping (non- articulated) fume arms are suited for booth-type welding which provides ease of use and improved operator breathing zone isolation.
Energy savings from reduced hp help pay for the system.
The end result is significant energy savings from reduced hp need and operator breathing zone protection due to constant airflow to fume exhaust arms.
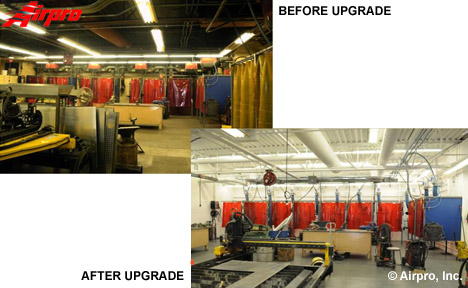