Production facilities that manufacture or process wood products face unique challenges with dust collection.
Woodworking facilities may cover a wide range of shops, from school woodshops to furniture production, to large scale enterprise production plants and lumber mills. Engineering for proper wood dust filtration and collection keeps workers safe and production running smoothly.
Challenges For Wood Processing Plants
Here are some of the main considerations for design of a dust collection system in wood industries.
Sawdust is a combustible dust hazard
Under the right conditions, sawdust can cause a fire or explosion, particularly fine sawdust, which is a combustible dust.
The National Fire Protection Association (NFPA) defines a combustible dust as:
“a combustible particulate solid that presents a fire or deflagration hazard when suspended in air or some other oxidizing medium over a range of concentrations, regardless of particle size or shape.”
The NFPA 652 standard states that that owners of woodworking production facilities must do a Dust Hazard Analysis (DHA) every five years.
Removing small wood particulate from the air in the production shop will reduce the probability of spontaneous fire or explosion.
Small particles of sawdust stay in the air for a long time
A five-micron particle of sawdust can stay floating in the air for up to thirty minutes. This dust can be breathed in by workers, where it can accumulate and cause respiratory diseases. Dust particles less than 10 microns pose the greatest health risks to workers. Dust that is aloft can also contribute to a potential explosion or fire situation.
Machine equipment collection ports and proper sizing
The efficacy of a dust collection system in a wood industries facility depends on correctly calculating the size of collection connection or port, minimum CFM required for collection, and static pressure loss in ducting. Choosing the wrong size in connections, ducting, or using too low a CFM will affect the dust collection and air filtration potential of the system.
Isolating the dust collector and ducting
A common setup for dust collection in woodworking shops is to capture the sawdust into a cyclone dust collector, or using a cyclone to separate the large and small particule where the smaller particulate is then fed into a baghouse dust collector. This allows the size of the bag house to be decreased for a lower dust volume.
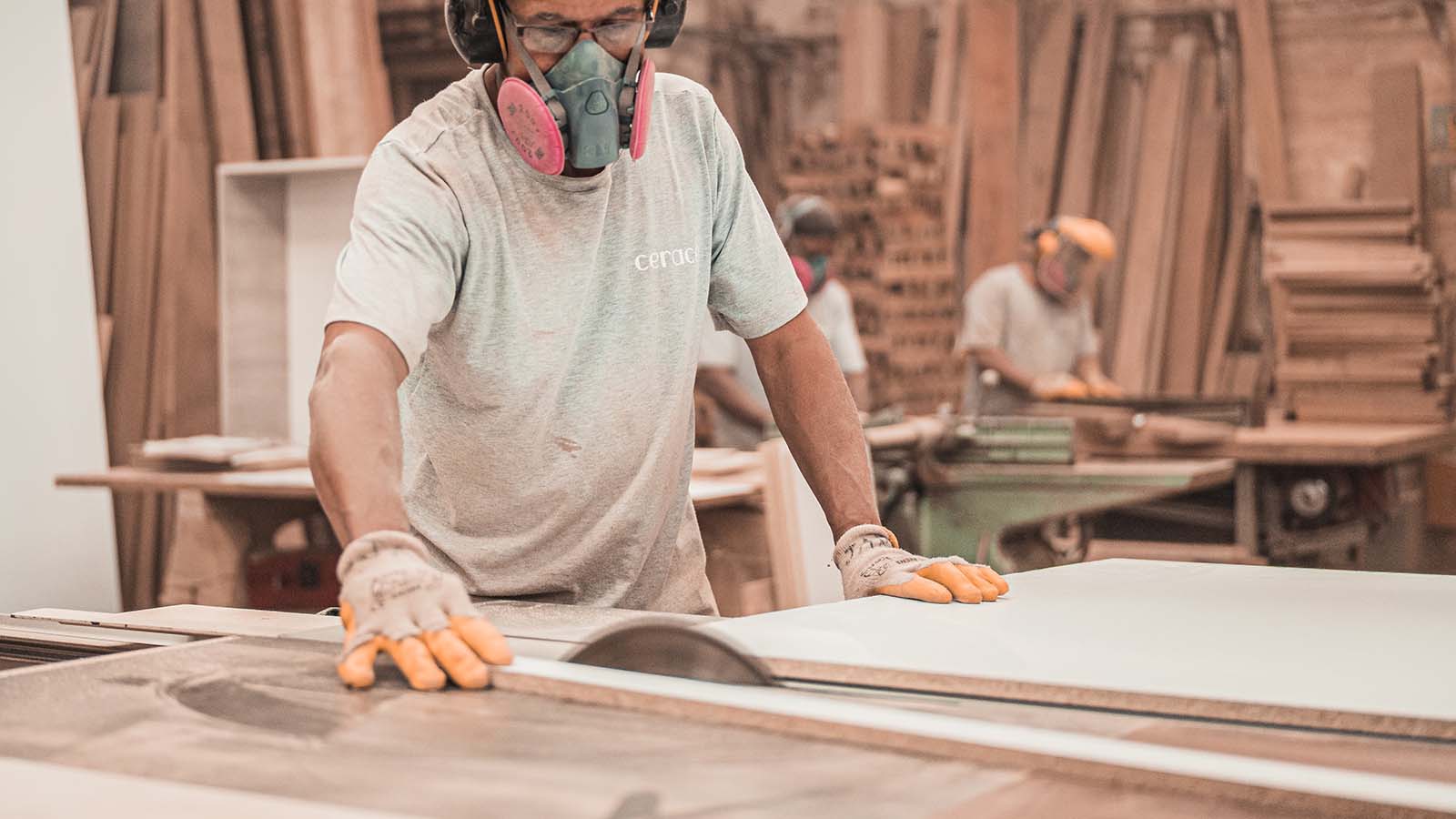
Needs of Wood Industries
Explosion protected equipment meeting NFPA standards
Dust collection systems in wood industry plants should also have explosion protection and fire mitigation equipment in place to prevent spontaneous fires and explosions.
Additional housekeeping equipment for clean-up in shop environments is also recommended.
Keeping the woodworking shop free of sawdust helps extend equipment life, reduces ambient dust in the air, and protects worker’s health. Many dust explosions occur when dust settles on surfaces, and an event propels the dusts into the air, where it is ignited by a spark source. Maintaining good housekeeping is a best practice for safety in wood and paper plants.
Central collection systems for production and manufacturing
Centralized dust collectors are used for industrial dust collection applications.
A centralized dust collector consolidates the cyclone and bag-house technologies into one dust collector. These centralized dust collectors remove hazardous dust and small particulate from the work environment, improving the overall air quality of the facility workspace.
Proper filter and dust collector configuration based on equipment needs
When your dust collection system has the correct filters, configuration, and CFM, the maximum amount of dust particles will be collected.
Source capture hoods to supplement machine connections
Source capture involves utilizing hoods to extract the dust particulate near the generation source to protect the worker and prevent the fine sawdust from migrating to other areas in the facility.