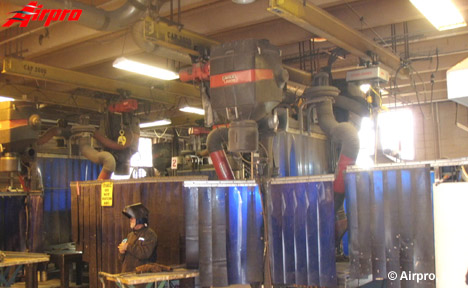
Application: Production Welding/Metalworking Department Air Filtration System upgrade. In order to meet safe interior operating conditions.
Dust Type: Welding Smoke and Grinding Dust
Location: Colorado
Airflow/Static Pressure: 4200 cfm @ 16” s.p.
Application Solution: Existing system consisted of (4) Lincoln Brand, 2 hp intermittent duty air filtration Units with manual clean filters and articulated fume exhaust arms. Intermittent duty filter units loaded with dust rapidly resulting in increased filter pressure drop and reduced airflow. Replacement filters were costly and the replacement task was tedious.
The new system was designed to power any 4 welding positions operating simultaneously. This was accomplished by using Nederman Auto Dampers controlled by current sensors located at each welding machine.
The Downflo Oval continuous duty dust collector keeps hood airflow constant because filters are cleaned on place while the system operates. This feature prolongs filter life thereby reducing filter replacement costs and task frequency. The combination of VFD, auto dampers and current sensors control airflow by opening/closing only when current flow is sensed. The telescoping fume exhaust arms are suited for booth-type welding which provides ease of use.
Significant energy savings from reduced hp need and operator breathing zone protection due to constant airflow to fume exhaust arms resulted.

