Industrial Cartridge Dust Collectors
Cartridge dust collectors are ideal for filtering fine particulate, in applications like plasma cutting, welding, grinding, food processing, and cosmetics production. Cartridge filters are pleated, in a cylindrical shape, and allow more filtering capacity per cubic foot of air than baghouse collectors. Most cartridge dust collectors use a pulse jet cleaning cycle to deposit collected particulate into a hopper.
Applications
- Grain and Agriculture
- Welding
- Laser Cutting and CNC Machining
- Material Handling
- Metalworking
- Thermal Spraying
- Abrasive Blasting
- Fiberglass Production
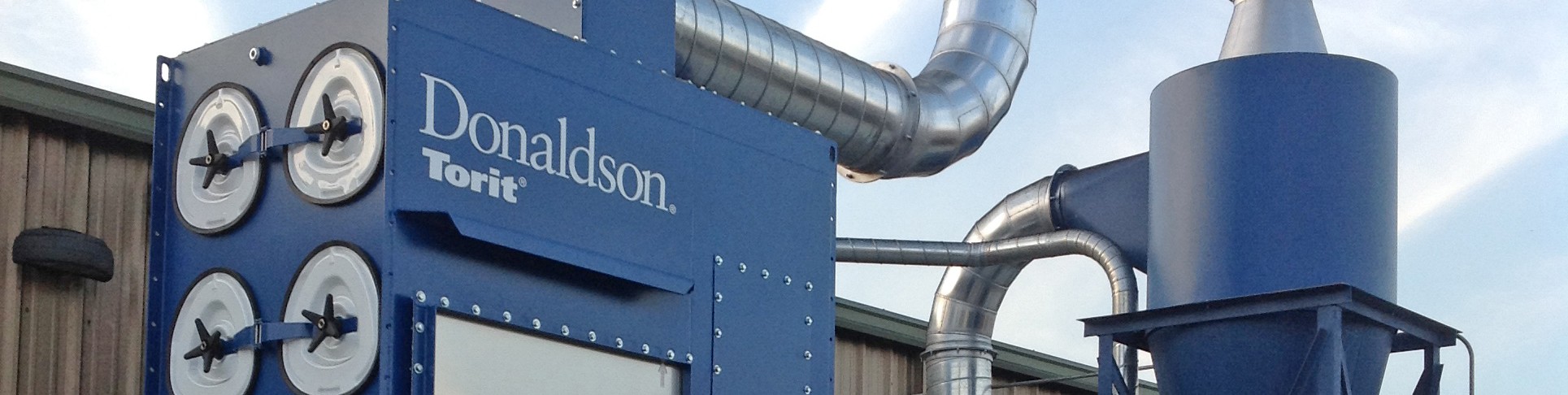
Brands
- Donaldson Torit
- Airflow Systems, Inc.
- IVEC Systems
- Nederman
How Cartridge Dust Collectors Work
In a cartridge dust collector, a fan moves dirty air into the area where the filters reside, called the dirty air plenum. Air moves through the filters, trapping dust and particulate on the outside of the pleated filters. These filters may be coated with spunbound or nanofiber material, to trap incredibly small particulate. Some filters are designed to be water or oil resistant.
The filtered air moves to the other side of the dust collector, into the clean air plenum, and exits the collector. Cartridges may be positioned horizontally or vertically, depending on the design of the collector. The cartridges are sealed with gaskets against a sheet of metal known as the tube sheet. Cartridge dust collectors generally have a better air to cloth ration than baghouse collection systems.
Cartridge dust collectors use pulse jet cleaning to remove accumulated dust from the filters. Short bursts, or pulses, of compressed air travel down the filter in the opposite direction from the flow of dirty air. These pulses knock the particulate off the filter and into a collection hopper.
Don’t See What You’re Looking For?
Other Custom Solutions Are Available
Contact an applications specialist to get help with an air filtration solution for your facility or plant.